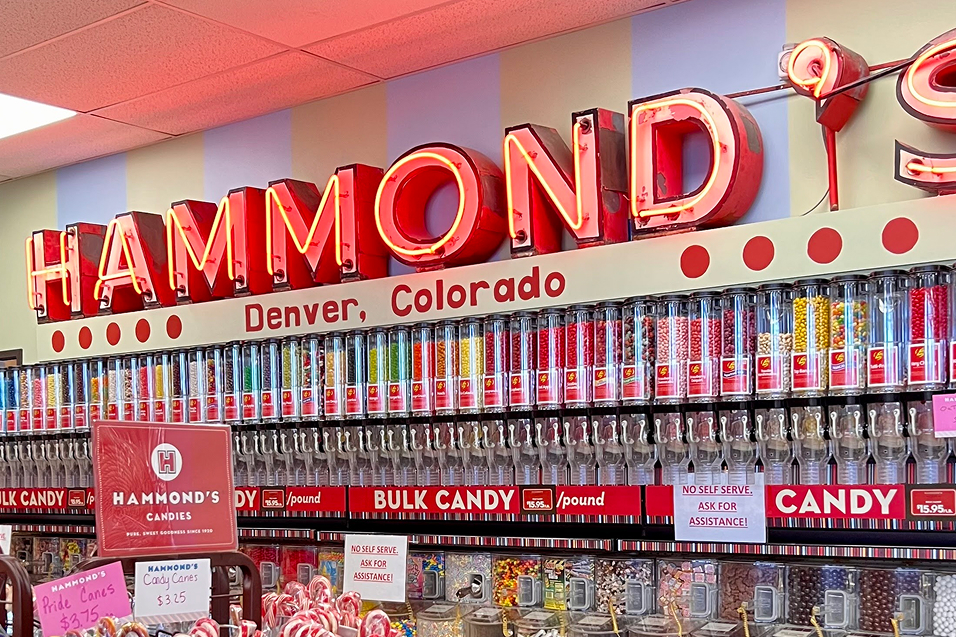
Hammond’s Candies Improves Efficiency and Accuracy While Cutting Costs by Going Digital With Allera
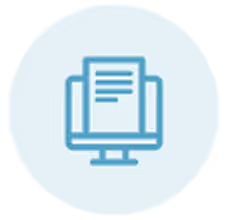
in SQF Audit Time
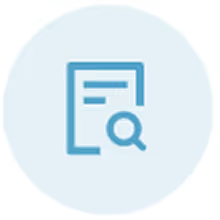
in Time to Search
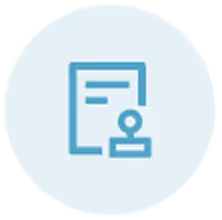
Converted to Digital
Paperwork Platform Problem
Hammond's Candies, a renowned confectionery manufacturer, has been in service for over a century. However, as the company grew, the company faced persistent challenges in managing and documenting their quality assurance (QA) and production paperwork. The traditional paper-based system they relied on led to inefficiencies, inaccuracies, and delays in recording crucial data. This manual approach hindered their ability to maintain consistent quality standards, resulting in occasional errors and difficulties in tracking production processes. Hammond’s Candies recognized the urgent need to transition to a digital solution to streamline their QA and production documentation.
“Working with Allera has been a great experience. The software is already improving our production and receiving processes, helping us modernize and boost efficiency. What really sets Allera apart is the team—they’re responsive, open to feedback, and committed to staying at the forefront of food safety and quality.”
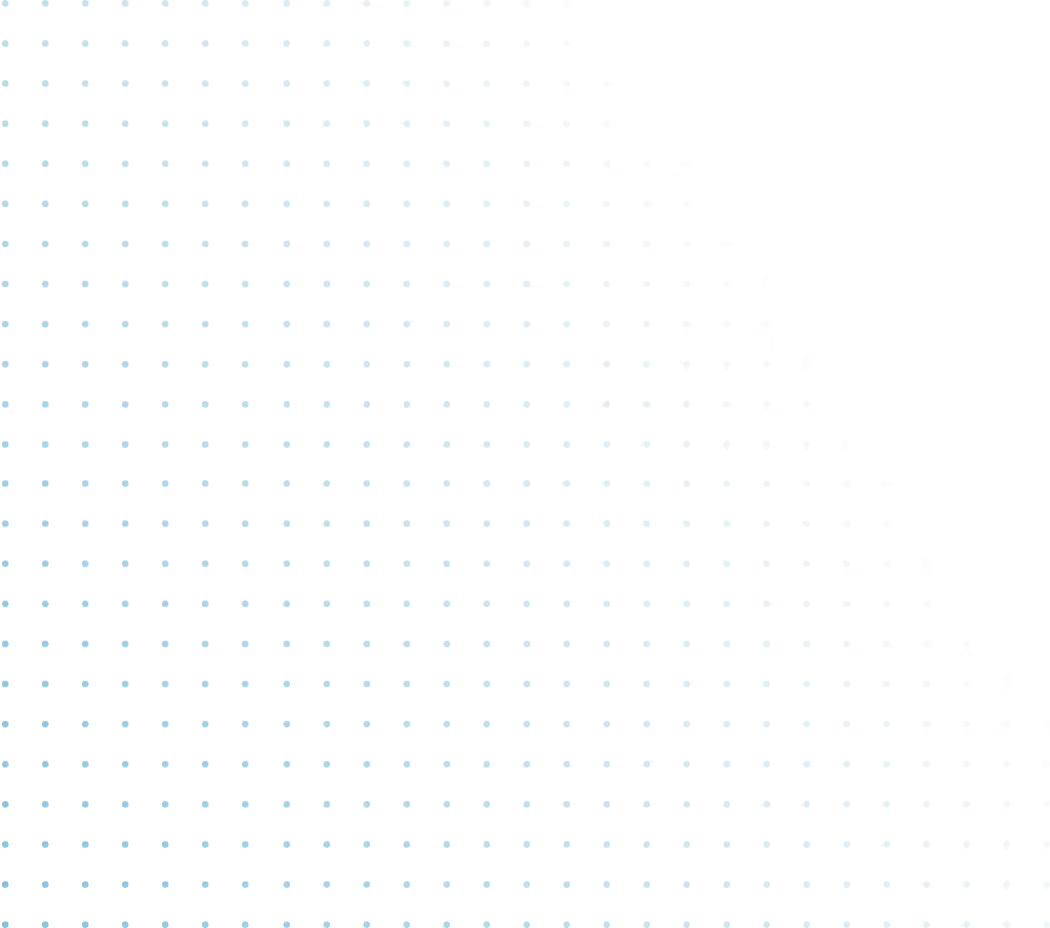
Solution
In response to these challenges, Hammond's Candies implemented Allera, a software platform tailored to digitize QA and production paperwork. Allera seamlessly integrated into Hammond's existing production workflows, providing a centralized hub for all documentation. The transition to Allera transformed Hammond’s Candies operations. The software’s user-friendly interface allowed for efficient data entry and real-time access to critical information, including quality control checklists, production reports, and supplier documents. Allera’s advanced analytics capabilities enabled managers to track trends, identify potential bottlenecks, and swiftly address any quality or compliance issues.
Results
The impact of Allera on Hammond's Candies' operations was remarkable:
Efficiency Gains
The adoption of Allera streamlined processes, reducing dozens of hours spent on paperwork. This allowed employees to focus more on core production activities, enhancing overall efficiency.
Accuracy and Compliance
With real-time data entry and automated documentation, Hammond's Candies experienced a notable reduction in errors. The software's automated alerts and reminders ensured that all necessary quality checks and compliance procedures were consistently followed.
Cost Savings
The company witnessed a reduction in operational costs related to paper usage, storage, and manual data entry. The optimized workflows resulted in significant savings in both time and resources.
Enhanced Decision-making
Allera's analytics and reporting capabilities provided actionable insights. Managers could make data-driven decisions, identify areas for improvement, and implement proactive measures to maintain high-quality standards.
Digital Transformation
Hammond's Candies successfully transitioned to a digital platform, reducing their reliance on paper-based documentation. This eco-friendly approach aligned with their commitment to sustainability.
Conclusion
Allera's integration into Hammond's Candies' production environment streamlined processes, elevated quality control measures, and ushered in a new era of efficiency and accuracy. The digital transformation enabled the company to stay competitive in the confectionery industry by ensuring consistent quality and compliance while reducing operational costs and environmental impact.